Technological description
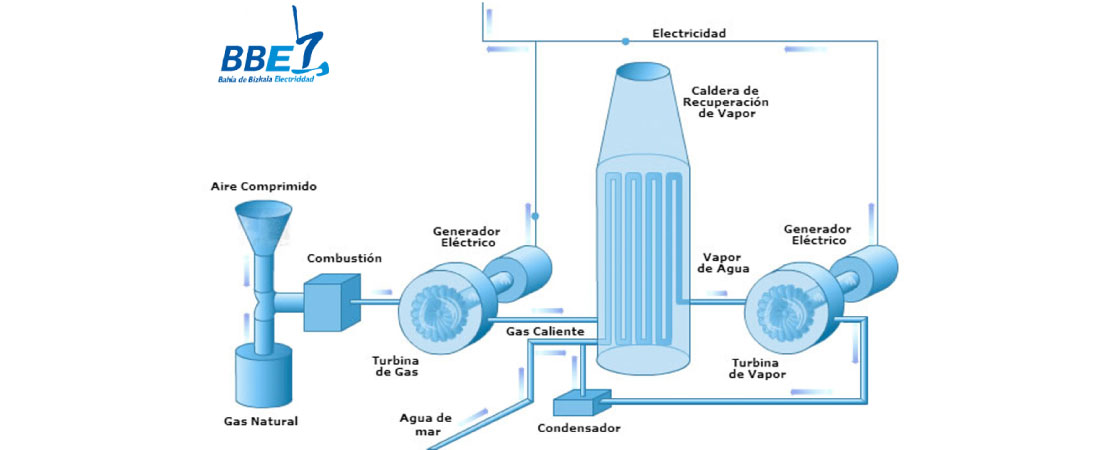
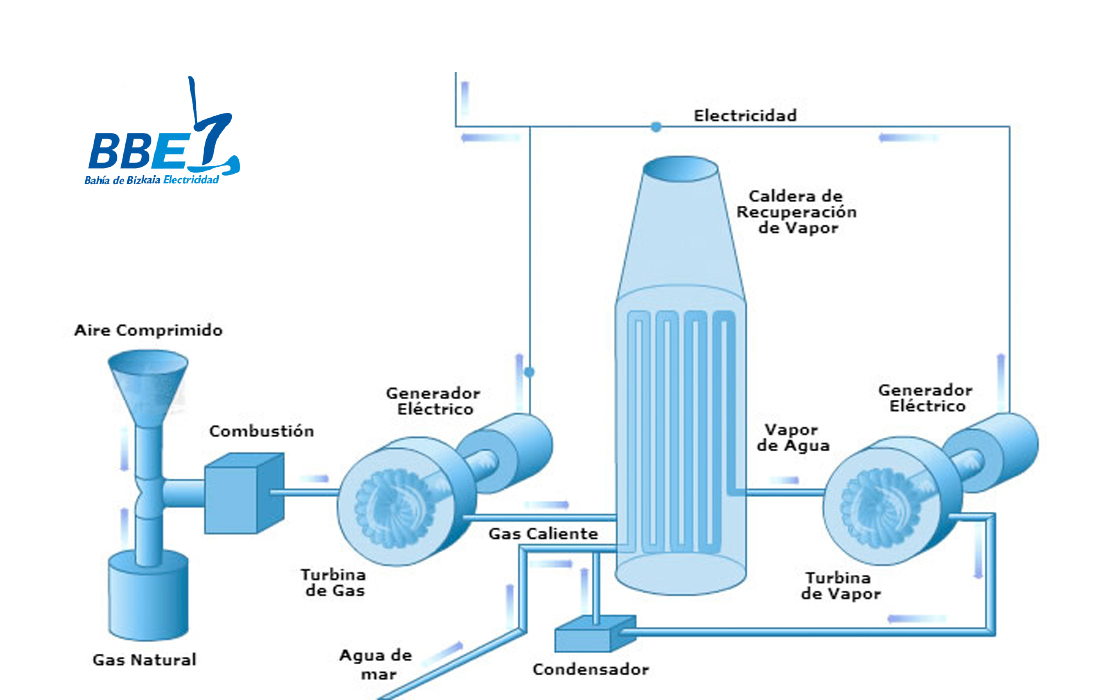
The combined cycle links an open gas turbine cycle (through a reheat boiler) with a closed steam turbine cycle, as shown in the figure.
Heat energy is provided in the form of fuel, natural gas, in the combustion chamber of the gas turbine. Here it is burnt with the comburent air previously compressed in the compressor.
The hot gases produced in the combustion chamber are conducted to the turbine, where they expand, driving the compressor and the generator simultaneously, and so creating electrical power. This part corresponds to what is called the “topping cycle”.
The main feature offered by the fuel mentioned is its high heat value, which allows greater efficiency in the thermodynamic cycle. Moreover, it is easy to handle and to mix with the combustion agent. Natural gas takes on a special importance in this process, as the exhaust gases from its combustion do not contain sulphur and, therefore, are cleaner.
The exhaust gases from the gas turbine, still hot, generate steam in the reheat boiler. This steam expands in the steam turbine and drives the generator in order to produce electrical power. This part of the cycle is known as the “bottoming cycle”.
The reason for the rapid development of combined cycle plants is based on two main aspects:
- Air is a cheap available means that can be used at high temperatures without problems.
- The steam cycle is already well known in conventional power plants and is adapted thermodynamically so as to be used in the “bottoming cycle”.
- The components used in a combined cycle are also used in other plants, which means that their development costs are low. In recent years, gas turbines have been developed until they achieve high gas intake temperatures, allowing very high performance levels to be obtained.
There are two main causes why the performance in a real process is significantly lower than the ideal performance of Carnot:
- On the one hand, the contribution of energy to the process takes place with a high temperature difference. In a conventional cycle, the temperature of the fresh steam might be about 540ºC, whereas the temperature at the furnace of the boiler is between 1,750 and 2,250ºC.
- On the other hand, the temperature of the cold focus point is higher than the ambient temperature.
These two effects cause losses.
The interest of the combined cycle lies, as we have already said, in its being adapted to these two processes. It is practically impossible to optimise a single process in both directions; however, by combining two processes we can approach both ends, thus improving the result.
Taking into account that the combustion gases coming from the combustion chamber directly feed the gas turbine, with no type of heat exchanger, therefore being required, the energy can be supplied at a very high range of temperatures. Nevertheless, it releases the energy at relatively high temperature into the atmosphere. This fact, which is so decisive in a single cycle plant, is not so in a combined cycle facility, as this energy is recovered in another cycle. The steam cycle retrieves this energy and uses it in its turbine and, although this does not work at a high temperature, it is capable of transferring the surplus energy at a temperature very close to ambient temperature, thus minimising losses. The combination, therefore, improves the performance and beat the expectations of any other single cycle.
Aunque en los ciclos reales no se llega, por supuesto, a esos rendimientos, sí da una idea de las posibilidades de cada proceso. Se aprecia que el ciclo combinado tiene un rendimiento muy superior a uno simple tan desarrollado e implantado como es el ciclo convencional con recalentamiento. Por otro lado, las pérdidas en el ciclo combinado son superiores debido a que el acoplamiento de los dos ciclos se produce con una diferencia de temperatura relativamente importante.Although these performance levels are not reached in real cycles, of course, it gives an idea of the possibilities of each process. It can be appreciated that the combined cycle offers a much higher performance than a single cycle, even one which is so developed and introduced simple as the conventional cycle with reheating (superheating), On the other hand, the losses in the combined cycle are higher due to the fact that the connection of the two cycles takes place with a relatively important temperature difference.
Naturally, the efficiency levels of any real cycle are lower that the ideal ones, due to losses. These losses can be of two types: energy losses, i.e. heat losses due to radiation and convection; and energy losses caused by irreversible processes in accordance with the second law of thermodynamics.
On the other hand, the Sankey diagram is a graphical way of representing the total balance of the energy involved in a thermodynamic cycle. Therefore, it represents the conversion of energy that takes place from the energy available in the fuel at the intake, through to the final production. This can be in the form of electrical or mechanical energy, depending on the case, taking into account all the losses that take place throughout the cycle.
Quantities are represented both in overall amounts and in percentages of the calorific value of the fuel.
In the case of combined cycles, the terms that appear in this kind of diagram are:
- Fuel intake heating power measured from the lower heat value.
- Electrical output obtained at the generator or generators of the gas cycle.
- Electrical output obtained at the generator of the steam cycle.
- Mechanical and heat losses, by radiation, at the reheat boiler.
- Heat losses in the exhaust gases at the flue of the reheat boiler.
- Mechanical and electrical losses at the generators of both the steam cycle and the gas cycle.
- Heat losses in the condensation water of the condenser.
- Power consumed by the plant itself.